What is Porosity in Welding: Ideal Practices for Avoiding Porous Welds
What is Porosity in Welding: Ideal Practices for Avoiding Porous Welds
Blog Article
Porosity in Welding: Identifying Common Issues and Implementing Finest Practices for Avoidance
Porosity in welding is a pervasive problem that frequently goes unnoticed until it creates substantial troubles with the honesty of welds. This typical defect can compromise the toughness and toughness of bonded frameworks, presenting security dangers and causing expensive rework. By recognizing the origin of porosity and carrying out effective prevention techniques, welders can dramatically improve the quality and reliability of their welds. In this conversation, we will certainly check out the essential aspects adding to porosity development, analyze its destructive effects on weld performance, and review the most effective techniques that can be adopted to decrease porosity incident in welding procedures.
Usual Root Causes Of Porosity
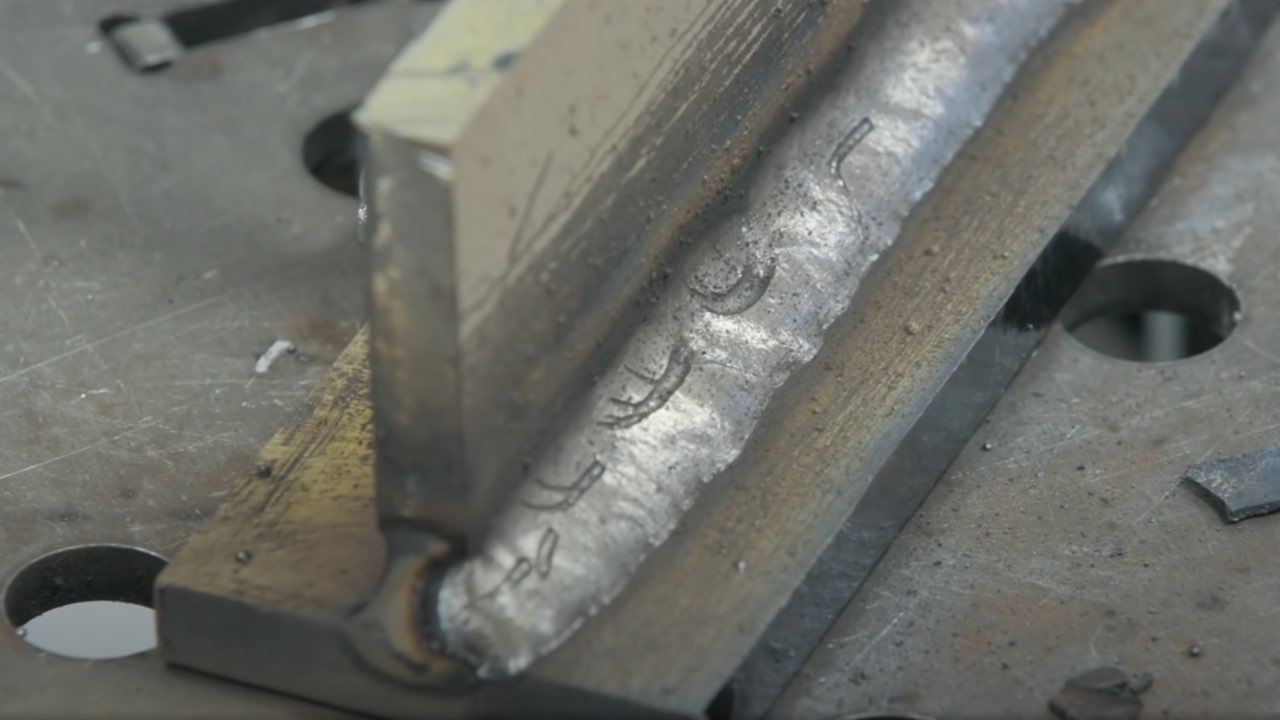
An additional constant offender behind porosity is the presence of impurities externally of the base steel, such as oil, grease, or corrosion. When these pollutants are not efficiently gotten rid of prior to welding, they can vaporize and come to be caught in the weld, causing flaws. Furthermore, making use of filthy or damp filler products can present impurities right into the weld, contributing to porosity concerns. To reduce these common reasons for porosity, detailed cleaning of base metals, appropriate shielding gas selection, and adherence to optimal welding specifications are essential methods in accomplishing high-grade, porosity-free welds.
Effect of Porosity on Weld High Quality

The presence of porosity in welding can dramatically jeopardize the architectural honesty and mechanical homes of welded joints. Porosity creates spaces within the weld steel, weakening its total strength and load-bearing capability. These voids function as tension concentration points, making the weld a lot more vulnerable to fracturing and failing under used loads. Additionally, porosity can decrease the weld's resistance to corrosion and various other ecological aspects, better reducing its longevity and efficiency.
One of the key consequences of porosity is a reduction in the weld's ductility and strength. Welds with high porosity degrees wikipedia reference tend to exhibit lower effect toughness and reduced ability to deform plastically prior to fracturing. This can be particularly worrying in applications where the bonded elements undergo vibrant or cyclic loading conditions. In addition, porosity can hinder the weld's capacity to effectively transfer forces, causing early weld failure and potential security threats in essential frameworks.
Ideal Practices for Porosity Prevention
To boost the structural integrity and quality of welded joints, what particular steps can be carried out to decrease the incident of porosity during the welding procedure? Using the right welding technique for the specific product being bonded, such as adjusting the welding angle and gun placement, can further stop porosity. Regular inspection of welds and immediate remediation of any type of issues identified during the welding procedure are necessary techniques to prevent porosity and produce high-grade welds.
Value of Correct Welding Techniques
Implementing appropriate welding strategies is critical in making certain the structural honesty and quality of welded joints, constructing upon the foundation of effective porosity prevention measures. Extreme warmth can lead to increased porosity due to the entrapment of gases in the weld pool. Additionally, making use of the ideal welding criteria, such as voltage, existing, and travel speed, is important for attaining audio welds with minimal porosity.
Furthermore, the selection of welding procedure, whether it be MIG, TIG, or stick welding, need to straighten with the specific requirements of the job to make sure ideal outcomes. Correct cleansing and preparation of the base steel, in addition to choosing the appropriate filler material, are additionally find out this here important components of competent welding strategies. By sticking to these ideal methods, welders can lessen the danger of porosity formation and produce top quality, structurally audio welds.

Examining and High Quality Control Steps
Testing check my reference treatments are necessary to discover and stop porosity in welding, making certain the toughness and longevity of the last product. Non-destructive testing approaches such as ultrasonic screening, radiographic testing, and aesthetic inspection are commonly used to recognize possible issues like porosity.
Post-weld assessments, on the various other hand, analyze the final weld for any kind of flaws, including porosity, and confirm that it fulfills specified standards. Carrying out a comprehensive high quality control plan that includes detailed screening procedures and inspections is vital to lowering porosity concerns and making sure the general quality of welded joints.
Verdict
Finally, porosity in welding can be a common concern that impacts the quality of welds. By identifying the common reasons of porosity and executing finest methods for avoidance, such as correct welding strategies and screening actions, welders can make certain excellent quality and reputable welds. It is important to prioritize prevention methods to reduce the occurrence of porosity and preserve the stability of welded structures.
Report this page